Fabricad [MRP]
material Requirements Planning Made Simple
MRP | MAINTENANCE | PLM | QUALITY CONTROL | INVENTORY | PURCHASING
Fabricad MRP
MRP stands for Material Requirements Planning. It is a methodology used in manufacturing and production management to determine the materials and quantities needed for the production process. The goal of MRP is to ensure that the right materials are available at the right time to meet production demands while minimizing inventory costs.
By implementing MRP, manufacturers can streamline their production processes, reduce inventory carrying costs, avoid stockouts, and improve overall efficiency. The MRP system acts as a planning tool that enables organizations to optimize material flow and ensure timely production.
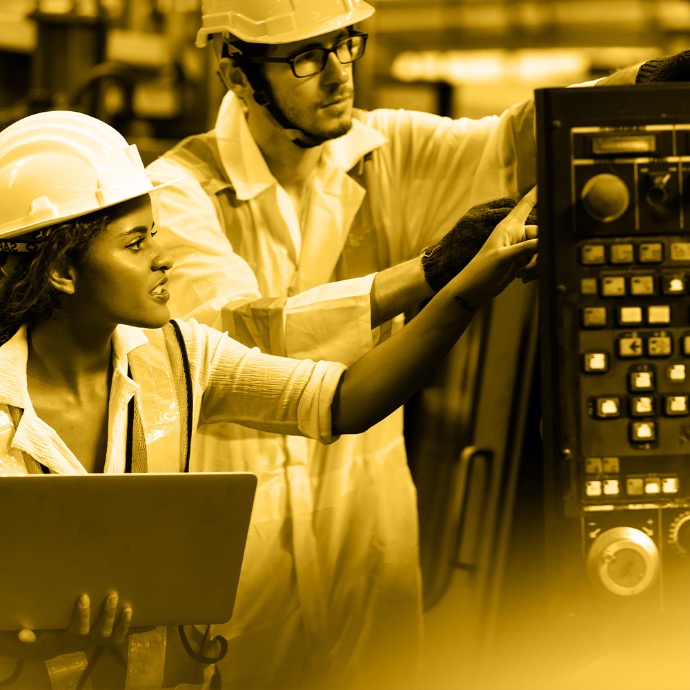
HOW MRP WORKS
Bill of Materials (BOM):
A BOM is a list that specifies the components or raw materials required to manufacture a product. It outlines the hierarchical structure of the product, detailing the quantity and relationships between the materials.
Master Production Schedule (MPS):
The MPS is a plan that specifies the production quantity and timing for finished products. It serves as a starting point for the MRP process.
Gross Requirements:
The MRP system determines the gross requirements by analyzing the MPS and BOM. It calculates the total quantity of materials needed based on the production schedule.
Net Requirements:
Net requirements are derived by subtracting the available inventory from the gross requirements. If the inventory is insufficient to meet the demand, a shortage is identified.
Planned Orders:
To fulfill the net requirements, planned orders are generated for each component or raw material. These planned orders indicate when and how many units of each material should be ordered or produced.
Purchase Orders and Production Orders:
Based on the planned orders, purchase orders are generated for external suppliers to procure the required materials. For internal production, production orders are created to initiate the manufacturing process.
Lead Times and Scheduling:
MRP considers the lead times associated with procurement and production activities. Lead times represent the time required to acquire materials or complete manufacturing tasks. By incorporating lead times, MRP helps determine the appropriate timing for placing orders or initiating production.
Tracking and Updating:
As materials are received or produced, the MRP system updates the inventory levels and adjusts the net requirements accordingly. This ongoing tracking ensures that the system maintains an accurate picture of material availability and demand.
Everything you need in one turnkey solution
Engineering
- PLM
- Bill of Materials
- Versioning
Manufacturing Engineering
- Routings
- Worksheets
Quality Control
- Control Points
- Checks (SPC)
- Alerts
Manufacturing
- Planning
- Control Panel
- Work Orders
Maintenance
- Equipment Management
- Maintenance Requests
Supply Chain
- MPS
- Routes
- Procurement Rules
Engineering
- PLM
- Bill of Materials
- Versioning
Manufacturing Engineering
- Routings
- Worksheets
Quality Control
- Control Points
- Checks (SPC)
- Alerts
Manufacturing
- Planning
- Control Panel
- Work Orders
Maintenance
- Equipment Management
- Maintenance Requests
Supply Chain
- MPS
- Routes
- Procurement Rules
Workcenter Control Panel
- Track Time
- Display Worksheets
- Register Production
- Integrate Quality checks
- In Process Alerts
- Record Serial/lot number
Optimize your inventory level
Through accurate fulfillment propositions
Use make-to-order rules, minimum stock rules or the master production schedule to automate procurements. Let the scheduler compute everything for you. Use routes, constraints and lead time to optimize inventory level and avoid shortages.
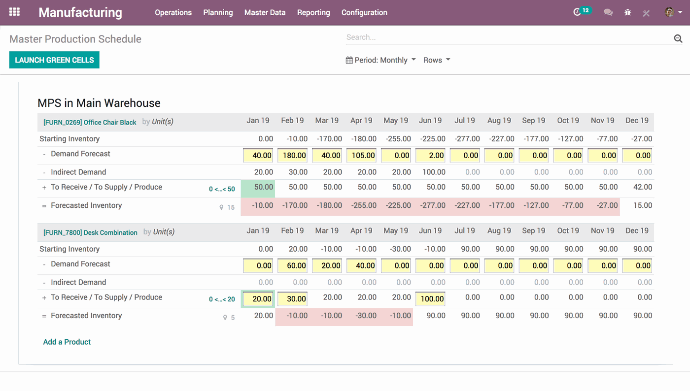
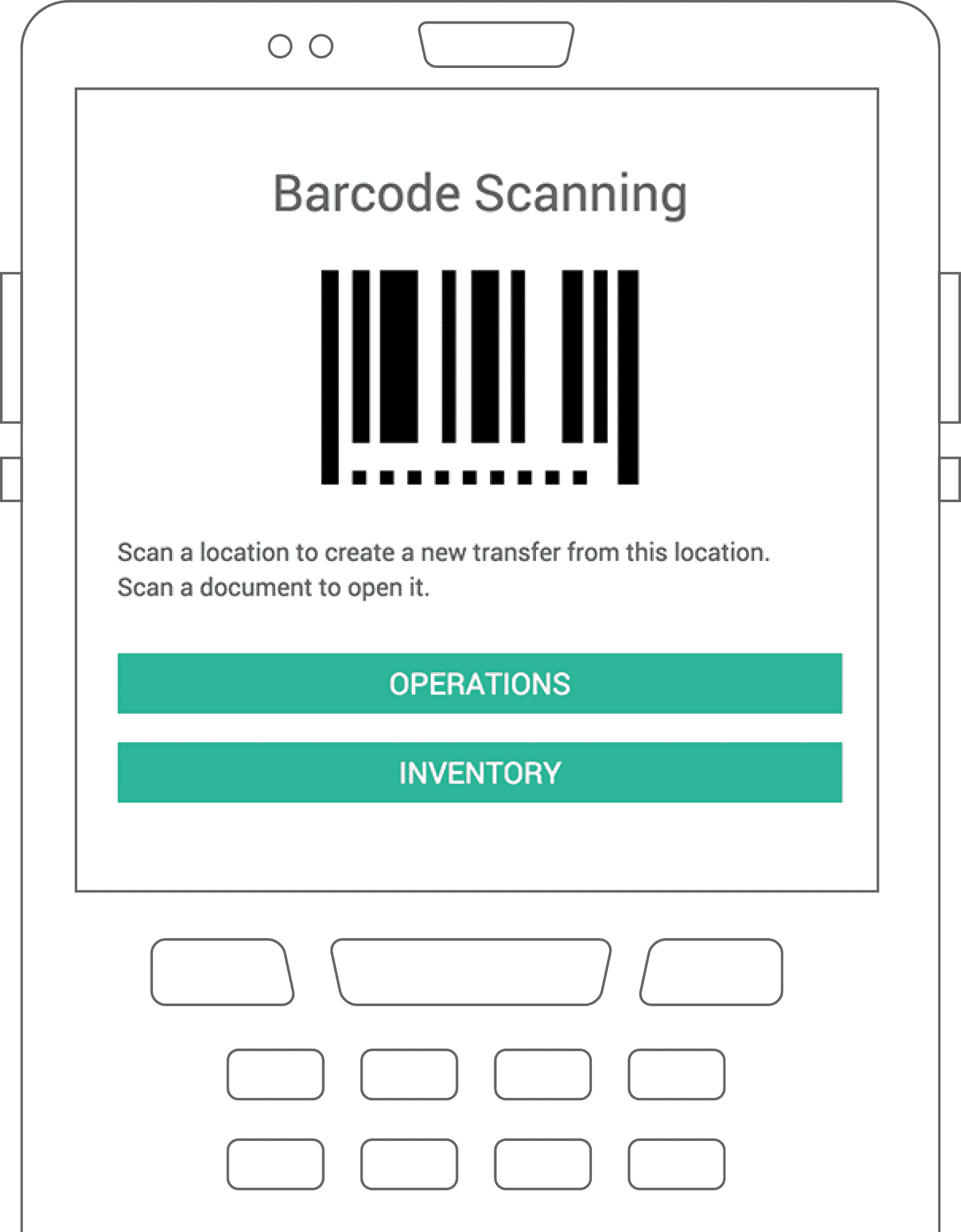
Optimize your inventory level
Through accurate fulfillment propositions
Whether you use lots, serial numbers or unidentified products, you can use barcodes to speed up operations at every step:
- Reception control
- Picking
- Packing
- Work orders
- ...and more!
Great Reporting & KPI
all the data you need, right at your fingertips
Control your productivity with real-time Overall Equipment Efficiency (OEE) reports and monitor the 6 big losses of TPM. Track maintenance KPIs like MTTR and MTBF. Create customized dashboards to monitor performance in real time.
Dynamic reports on everything from costing to traceability, performance analysis, OEE, and more help you make smarter decisions about your business.